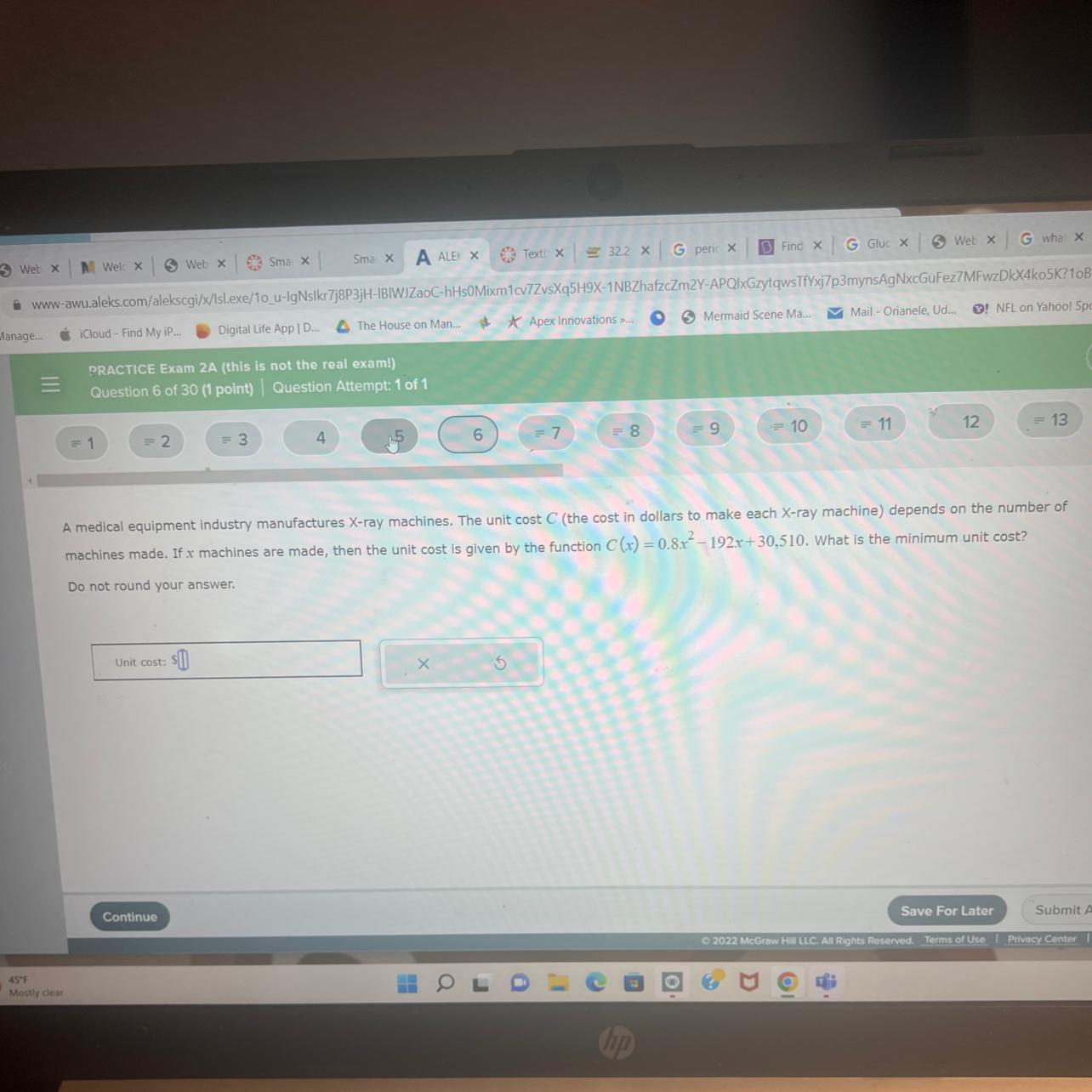
In the world of manufacturing, the concept of unit cost is critical to understanding profitability and efficiency. When we say "if x machines are made, then the unit cost is given by the," we are delving into the economics of production and how various factors influence the cost per unit of output. This article will explore the intricacies of unit cost, the factors affecting it, and practical applications in real-world scenarios.
As businesses scale their production efforts, understanding how to calculate unit costs becomes essential. Not only does it provide insights into operational efficiency, but it also aids in pricing strategies, budgeting, and financial forecasting. Therefore, grasping the relationship between the number of machines produced and the unit cost is vital for any manufacturing entity.
In this comprehensive article, we will discuss the various components that contribute to unit cost, the formula used to calculate it, and the implications of these costs on business strategies. By the end of this article, you will have a robust understanding of how unit costs are determined and how they can be optimized.
Table of Contents
What is Unit Cost?
Unit cost refers to the total expenses incurred to produce a single unit of a product. It includes all costs associated with manufacturing, which can be broadly categorized into fixed costs and variable costs.
Fixed Costs
- Depreciation of machinery
- Rent for manufacturing facilities
- Salaries of permanent staff
Variable Costs
- Raw materials
- Direct labor costs
- Utilities based on usage
Factors Affecting Unit Cost
Several factors influence the unit cost of production. Understanding these can help manufacturers make informed decisions to optimize costs.
Production Volume
Generally, as production volume increases, the unit cost decreases due to the spreading of fixed costs over a larger number of units.
Economies of Scale
- Bulk purchasing of raw materials
- Efficient use of production resources
- Specialization of labor
Calculating Unit Cost
The formula for calculating unit cost is straightforward:
Unit Cost = (Total Fixed Costs + Total Variable Costs) / Total Units Produced
Let’s break this down further with an example:
- Total Fixed Costs: $100,000
- Total Variable Costs: $50,000
- Total Units Produced: 5,000
Using the formula, the unit cost would be:
Unit Cost = ($100,000 + $50,000) / 5,000 = $30
Importance of Unit Cost in Manufacturing
Understanding unit cost is crucial for several reasons:
- Pricing Strategy: Helps in setting competitive prices.
- Profitability Analysis: Aids in determining the profit margin.
- Cost Control: Identifies areas for cost reduction.
Case Study: Impact of Production Volume on Unit Cost
Let’s examine a hypothetical case study to see how production volume affects unit costs.
Company A manufactures widgets. In their first year, they produce 1,000 units with a total cost of $50,000. The unit cost is:
Unit Cost = $50,000 / 1,000 = $50 per unit
In the second year, they scale production to 5,000 units. The total cost remains at $50,000 due to fixed costs. The new unit cost is:
Unit Cost = $50,000 / 5,000 = $10 per unit
This significant drop illustrates how increasing production can lower unit costs, allowing for more competitive pricing.
Strategies to Reduce Unit Cost
To maintain profitability, manufacturers can adopt various strategies to lower unit costs:
- Invest in technology to improve efficiency.
- Negotiate better rates for bulk purchases of materials.
- Streamline operations to minimize waste.
Real-World Examples of Unit Cost Calculation
Many successful companies have optimized their unit costs effectively. Consider these examples:
- Company B implemented automation, reducing their unit cost by 25%.
- Company C used lean manufacturing techniques to minimize waste and lower costs.
Conclusion
In summary, understanding the relationship between the number of machines produced and unit cost is vital for any manufacturing business. By focusing on the factors that influence unit costs and implementing strategies to reduce them, companies can enhance their profitability and market position. We encourage readers to share their thoughts in the comments below and explore more articles to deepen their understanding of manufacturing economics.
Thank you for reading. We hope you found this article informative and valuable for your manufacturing endeavors. Don't forget to visit our site for more insights and updates!
ncG1vNJzZmivp6x7rLHLpbCmp5%2Bnsm%2BvzqZmm6efqMFuxc6uqWarlaR8rq3CoaCnnaNiuqKwxGagn2WoYrqir8eipZ6rXZa%2FpnnMmpueZaSdsq9506GcZq2ensFur86sq2aho2K0qsLEp2SbsV2ptaZ6x62kpQ%3D%3D